Cuando aparecen holguras y las diferentes partes que componen el
timón dejan de ser solidarias, el timón
se notará blando e impreciso y finalmente acabará por romperse. Antes de que
esto ocurra apreciaremos rajas y señales de debilidad en la superficie
del timón, indicando la necesidad de una urgente reparación.
¿Por qué se rompe un timón?
Los esfuerzos y tensiones a los que está sometido un timón son
enormes, pues en ellos se soporta toda la fuerza capaz de hacer que
el barco cambie de rumbo. En cada cambio de dirección, las dos capas
de fibra del timón son comprimidas y sometidas a un desgaste por
"stress y fatiga" del material.
Si en una mala maniobra o en un paso con un mar demasiado somero
tocamos fondo, quizás sea el timón quien se lleve el golpazo. Las
causas de fallos pueden ser variadas y al final desembocan en
roturas de parte del timón, cojinetes de apoyo estropeados en el
tintero, o ejes doblados que impiden un giro libre de toda la
sección angular en la que debe trabajar el timón.
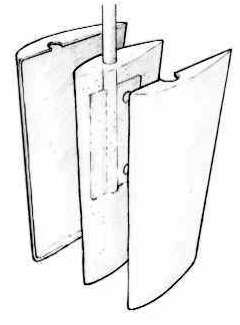
En otras ocasiones el fallo proviene de la degradación en que está
construido el "sandwith" del timón por un fenómeno de ósmosis. En
otros casos, por la parte superior de la pala se produce una holgura
entre el eje y el plano superior, por el que poco a poco va entrando
agua que empapa la espuma y produce una deslaminación de la piel
exterior del timón construida en fibra de vidrio. Esto último ocurre
con frecuencia en las latitudes frías, en donde en invierno el agua
puede expandirse con las temperaturas muy bajas y actuar como una
cuña que raja y destruye el timón desde el interior.
Este tipo de problemas requiere retirar la pala mediante una
suspensión en el travel lift y sanear el timón en profundidad, a
veces retirando totalmente la capa de fibra para alcanzar el
interior en el que debemos retirar la espuma antigua, darla forma y
relaminar desde cero.
Reparar la parte superior del timón
Cuando ya se ha producido una pequeña holgura entre el eje del timón
y la fibra, debemos reparar cuanto antes pues en las primeras fases,
la reparación es sencilla, pero si lo dejamos pasar, puede producir
serios problemas en el núcleo del timón. Lo más sencillo es aislar
con algún tipo de sellador epoxi, pero debemos retirar un poco el
material alrededor de este cuello, para que el material penetre en
profundidad y garantice la estanqueidad.
Si observáramos las fisuras en la parte superior de la superficie
del timón, el síntoma indica fallos por stress del material que se
irán extendiendo a medida que aumente la fatiga del material. Si son
pocos, debemos lijar con una máquina eléctrica en la zona afectada y
relaminar la zona con tejido biaxial y epoxi para posteriormente
superponer otra capa con un epoxi empapado en una carga de alta
densidad.
Sin lugar a dudas debemos repasar y arreglar la zona de unión del
eje con la superficie superior del timón y para ello, retiraremos
material alrededor del eje en donde debemos introducir tiras de
tejido de fibra de vidrio empapadas en epoxi y sellando la parte
superior con epoxi mezclado con una carga de alta densidad.
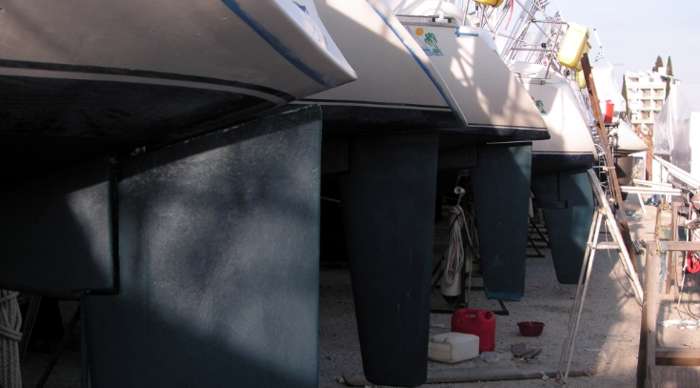
1. Lijamos
la parte dañada alrededor del eje agrandando la fisura con alguna
lijadora rotativa o herramienta tipo dremmel teniendo cuidado de no
dañar el eje de acero.
2. Si
es necesario se debe cortar y retirar algo de espuma para conseguir
un hueco con un ángulo de 45º en donde rellenaremos con nuevo
material.
3. Lijaremos
también la superficie superior del timón alrededor de esta apertura
en una banda de unos 2 centímetros desde el final del hueco que
hayamos efectuado.
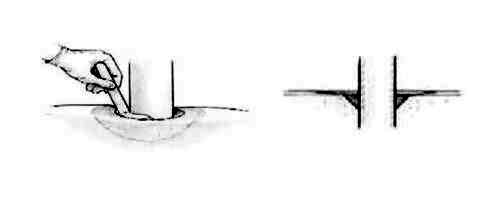
4. Debemos
secar la zona calentando con una manta eléctrica que dejaremos
actuar el tiempo necesario hasta que la parte afectada esté
totalmente seca.
5. Hay
que lijar un poco la superficie metálica del eje con grano 80, para
que el epoxi agarre bien y forme una unión solidaria.
6. Aplicamos
epoxi sin carga y laminaremos finas tiras de fibra de vidrio
empapadas en epoxi, hasta lograr rellenar casi la totalidad del
hueco que hemos abierto. Finalizamos el relleno con varias capas
formadas por tiras de tejido biaxial, más anchas, que monten sobre
la superficie horizontal que previamente habíamos lijado y rebajado
ligeramente con la lijadora.
7. Una
vez seco el laminado efectuado, debemos terminar de rellenar el
hueco mediante una masilla de epoxi que podemos realizar mezclando
resina epoxi con una carga de microesferas. Con una paleta
conseguiremos allanar el resultado y así ahorrar trabajo de lijadora
una vez seca la masilla.
8. Lijaremos
con grano 200 para conseguir una superficie de agarre que sirva de
soporte a un nueva capa de epoxi que actuará como barrera de acabado
y base a la pintura final.
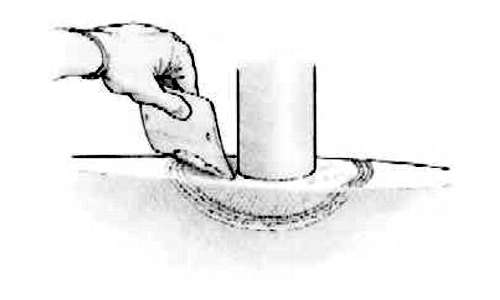
Reparar una deslaminación
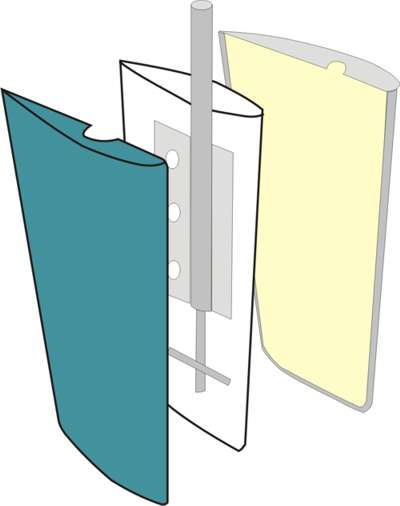
Cuando la superficie del timón ha acumulado demasiado esfuerzo por
trabajo y stress, pueden aparecer fisuras en la superficie del timón
especialmente en las zonas más cercanas a las extensiones metálicas
que trasladan el esfuerzo de giro del timón. Si el problema solo
afecta a estas fisuras, debemos sanear una a una o trabajar más en
profundidad si el tejido está seriamente deslaminado.
Aunque este tipo de problemas puede ocurrir en cualquier parte de la
superficie del timón, es más normal que aparezca en la zona donde
acaba el eje y los últimos refuerzos metálicos interiores. Cuando
las fracturas son muy evidentes, es casi seguro que el agua ya haya
penetrado al interior y haya comprimido la espuma que aunque sea de
núcleo cerrado habrá invadido el interior.
Al sacar el barco del agua y quedar varado, comprobaremos como el
goteo del timón dura muchas horas o incluso días, indicando sin duda
que debemos trabajar el interior del timón para abrir la zona,
secar, rellenar y curar.
Para ello debemos efectuar pequeños taladros de 3 ó 4 milímetros que
facilitarán el drenaje del agua que ha penetrado al interior. Con un
pequeño martillo de plástico, podremos golpear suavemente la
superficie del timón para identificar las zonas afectadas que
tendrán un sonido diferente al ser golpeadas. Las zonas deslaminadas
sonarán con un sonido mate fácilmente identificable y diferente a
los golpes realizados sobre el tejido sano. Con un rotulador debemos
ir marcando las zonas que están afectadas.
Si éstas son pocas y bien delimitadas, lo mejor es perforar con un
taladro para facilitar el secado y rellenarlos con epoxi. Si la zona
es amplia y está unifórmemente deslaminada, debemos cortar el tejido
afectado y eliminar y ahuecar la espuma empapada, para una vez seco y
limpio rellenar con nueva espuma y proceder a realizar un nuevo
laminado o a pegar la capa retirada si estuviera bien y pudiera ser
reutilizada para actuar como soporte al nuevo relaminado exterior.
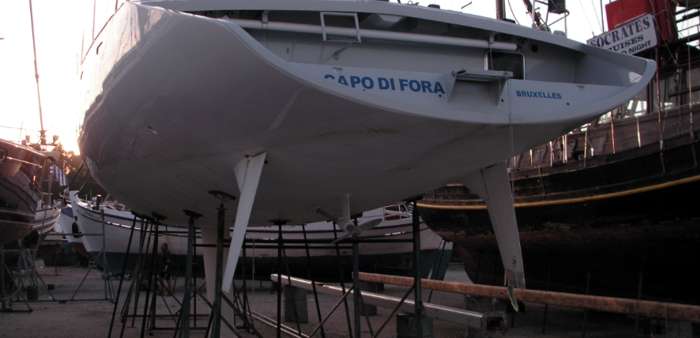
Perforar y rellenar los agujeros
Si la avería no es muy grande, el método de realizar perforaciones
para drenar y secar es sin duda el más sencillo y fácil de realizar.
Debemos perforar cada 2 ó 3 centímetros con una broca de 3
ó 4
milímetros, por lo que saldrá la humedad que empapa la espuma
interior. Debemos montar una "jaula" alrededor del timón para
calentarlo a unos 60ºC y conseguir por evaporación secar bien el
interior del timón. El proceso puede durar varias semanas hasta
conseguirse un secado completo, y puede ser menos efectivo que abrir
toda la superficie para sustituir la espuma por una nueva. Los
agujeros deben tener una profundidad suficiente para alcanzar más de
la mitad de la anchura de la pala en cada uno de ello y por tanto
llegar bien al núcleo de la espuma. Debemos estar atentos al
perforar pues podríamos toparnos con el eje o los refuerzos
estructurales metálicos interiores. Si esto ocurriera, no se preocupe,
y realice otra perforación a unos pocos centímetros.
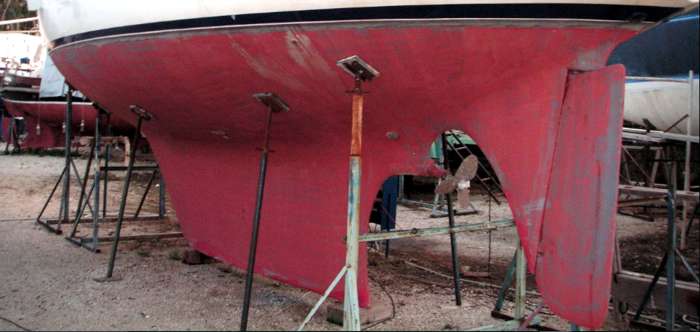
1.
Una vez totalmente
seco inyectaremos epoxi con ayuda de una jeringuilla hipodérmica.
Tenga en cuenta que el secado del núcleo interior puede durar
bastantes semanas incluso haciendo un buen número de perforaciones,
especialmente si lo hace al aire libre sin ayuda de calentadores.
2.
Una forma de
comprobar si se ha secado a fondo, es hacer un nuevo agujero y
comprobar si en él no se detecta ninguna nueva humedad, apretando un
poco el foam interior.
3.
Inyectaremos el
epoxi despacio, agujero por agujero, y con una temperatura
moderadamente baja para que la polimerización sea lenta y dé tiempo
a que el epoxi penetre completamente en todos los huecos y por todas
las zonas deslaminadas. El timón debe estar plano para que la
gravedad haga su trabajo y la resine ocupe todos los espacios
interiores.
4.
Si los agujeros han
sido muchos y muy próximos es conveniente acabar el trabajo con una
capa de tejido biaxial para lo que debemos lijar la superficie y
lograr un buen agarre de este laminado final.
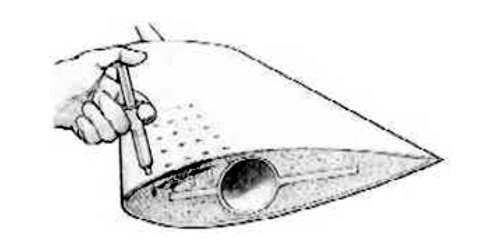
Retirar el laminado y cambiar la espuma interior
Se trata de un trabajo más importante y conveniente cuando los daños
han sido mayores. Debemos cortar con una pequeña radial la fibra de
vidrio en la zona deslaminada. Una vez retirado la "piel" exterior
accedemos a la espuma que debemos retirar con ayuda de un formón o
cualquier otra herramienta cortante.
Una de las ventajas de este proceso radica en no tener que esperar
semanas en conseguir secar el núcleo, pues este será sustituido con
nueva espuma. Al abrir totalmente el interior del timón
conseguiremos
reparar en profundidad y con seguridad, pues
vemos en detalle la extensión del problema existente. Las
superficies pueden ser secadas en cuestión de horas con la ayuda de
una pistola de calor y comenzar el trabajo de reconstrucción unas
horas después.
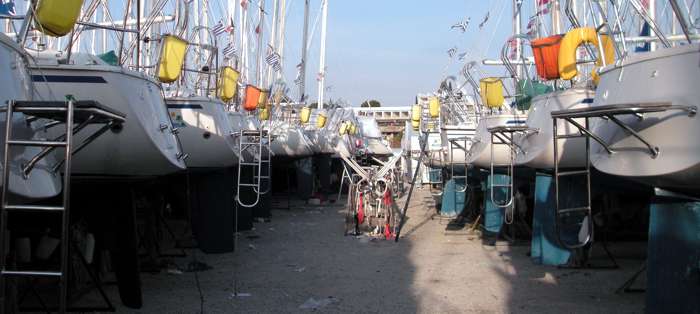
1.
Debemos cortar una
ventana que nos permita retirar la capa de fibra de vidrio. Para
ello una de las mejores herramientas en la radial pequeña con una
hoja fina de corte. Debemos tener cuidado en penetrar solo los pocos
milímetros de espesor de esta capa laminada, so pena de cortar los
refuerzos interiores que queremos dejar intactos. También es útil la
cortadora de vibración con sus diferentes accesorios para poder
cortar la fibra y para retirar la espuma estropeada en el interior.
2.
Arrancaremos la capa
de fibra con cuidado pues estará adherida a la espuma interior y
en
algunas ocasiones puede estar adherida a algún refuerzo interior.
3.
Ahora debemos eliminar toda la
espuma vieja y empapada de agua salada.
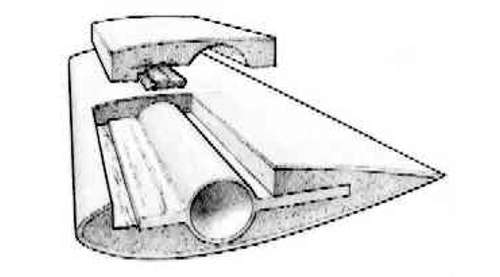
4.
Ha llegado el
momento de secar a fondo todo el interior del timón. Para ello
podemos utilizar un secador a aire, o focos de radiación infrarroja,
o una manta eléctrica colocada debajo de la pala. Debemos tener
cuidado, pues en cuanto se vaya perdiendo la humedad la temperatura
puede subir excesivamente.
5.
Debemos rebajar con una lijadora
el borde de la ventana para que el escalón quede convertido en una
rampa. Haremos lo mismo con la pieza de fibra retirada si esta fuera
a ser reutilizada para tapar el hueco realizado. De esta manera
cuando cerremos podremos laminar de forma escalonada para cerrar con
mucha fuerza la apertura realizada en la superficie del timón.
6.
Limpie a fondo todo
el vaciado mediante un aspirador y si fuera necesario, a
continuación, utilice un trapo empapado con acetona. Utilice guantes.
7.
Ahora comienza el
verdadero trabajo de reconstrucción. Lo mejor para rellenar la nueva
espuma es utilizar una espuma expansiva que consiste en dos
productos de aspecto mieloso y que al mezclarse comienzan a expandir
hasta varias veces el volumen inicial. No utilice espuma de
poliuretano en botes a presión del tipo utilizado en construcción
pues tiene una expansión demasiado rápida y densidad muy baja.
Necesitamos que la espuma de poliuretano utilizada expanda
lentamente para que podamos ‘mojar bien las superficies en donde ha
de crecer la espuma y de esta manera produzca una fuerte adherencia.
8.
No tenga problema si
la espuma crece mucho más de lo que la forma del timón indica. Al
cabo de un par de horas podremos eliminar la parte más importante
del sobrante con un cutter y proceder a lijar hasta conseguir la
forma que debe tener la pala.
9.
Cuando tengamos la
forma adecuada debemos ‘tapar’ la ventana abierta y para ello
podemos utilizar la misma pieza que cortamos y retiramos en los
primeros pasos, pero solo en caso de que esta ‘piel’ se encuentre en
buen estado y no muestre ningún signo de deslaminación.
Impregnaremos toda la parte interior de la pieza y la superficie de
la espuma con epoxi y procederemos al pegado, sujetando la pieza con
algún gato o gomas elásticas.
Tenga cuidado al mezclar el epoxi pues algunos de ellos producen una
reacción exotérmica durante la polimerización que elevará la
temperatura de la zona y en ocasiones puede subir demasiado. No
utilice cargas en esta fase del pegado o laminado.
10. Si hubiera sido
necesario crear un nuevo laminado, debemos calcular el número de
capas necesarias para conseguir un espesor equivalente al original.
El numero de capas puede varias mucho dependiendo del tamaño del
timón y no es raro tener que llegar a lamina de 6 a 8 capas, o
incluso más.
11. Ahora debemos
preparar un epoxi cargado con microesferas para conseguir una pasta
más densa que aplicaremos ayudados con una espátula para conseguir
suavizar la forma de la pala. Una vez seco lijaremos con lija de
grano 120 y marcaremos con un rotulador ayudados con una regla, las
zonas donde aún falte algo de relleno para conseguir una superficie
curva uniforme.
12. Por ultimo debemos
aplicar varias barreras de epoxi para impermeabilizar totalmente la
zona. No se olvide de lijar ligeramente con grano 200 la última capa
aplicada, para que pueda agarrar la pintura final o antifouling.
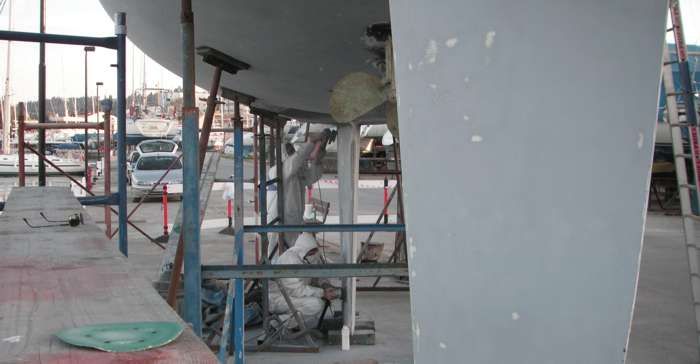
Artículos relacionados:
-
Reparar el timón de un
barco
-
Repara tu barco con
NovaBoats
-
Destrozar un cata por dormirse y cómo
recuperarlo totalmente